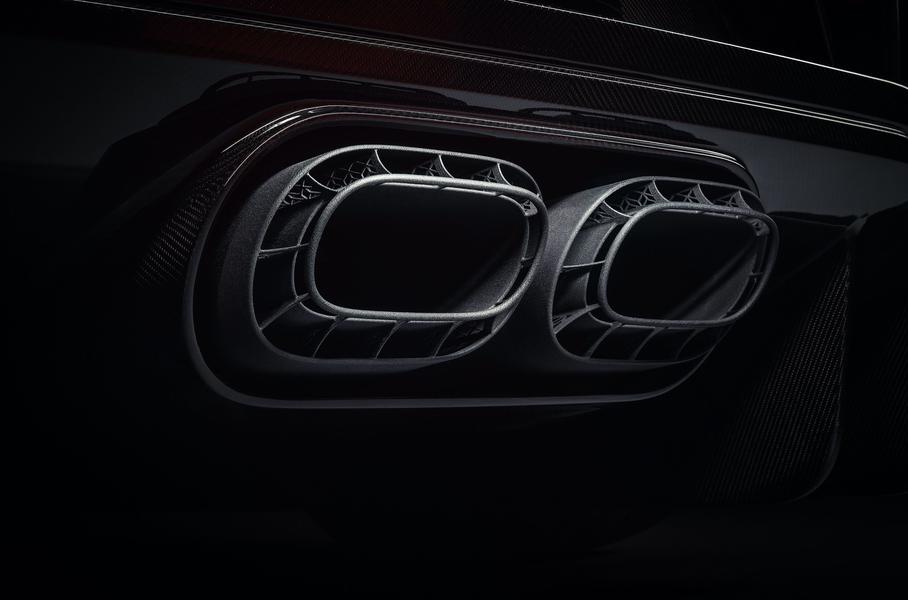
Компания Bugatti с 2018 года экспериментирует с 3D-печатными деталями и использует их на моделях Chiron Sport, Divo, La Voiture Noire и Centodieci.
Однако теперь французский производитель гиперкаров расширил область применения аддитивных технологий и впервые получил разрешение сертификационных органов на использование в дорожных машинах видимого элемента, напечатанного из титана.
С недавних пор Bugatti считается единственным автопроизводителем, печатающим наконечники выхлопных патрубков из титанового порошка.
Причем эти накладки впервые сертифицированы как видимый элемент конструкции дорожных машин. На Chiron Pur Sport размеры каждой такой детали следующие: длина, ширина высота — 22, 48 и 13 сантиметров соответственно.
Вместе с решеткой и скобой крепления насадка весит 1,85 килограмма, что на 1,2 килограмма меньше, чем та же самая деталь на простом «Широне».
В процессе печати задействованы четыре 400-ваттных лазера, спекающих 4200 слоев титанового порошка.
Технология позволяет создаваться элементы с минимальной толщиной стенок всего 0,4 миллиметра и внутренней «бионической ячеистой структурой».
А там, где это необходимо применяется «решетчатая структура», то есть пустоты заполняют крошечными распорками. Причем даже такой «филигранный» элемент, как титановая насадка, способен выдержать температуру в 650 градусов Цельсия.
Это достигается за счет двухуровневой внешней части, которая обеспечивает термическую изоляцию и заодно улучшает охлаждение.